How to Make Your Utility Rig Compliant and Audible
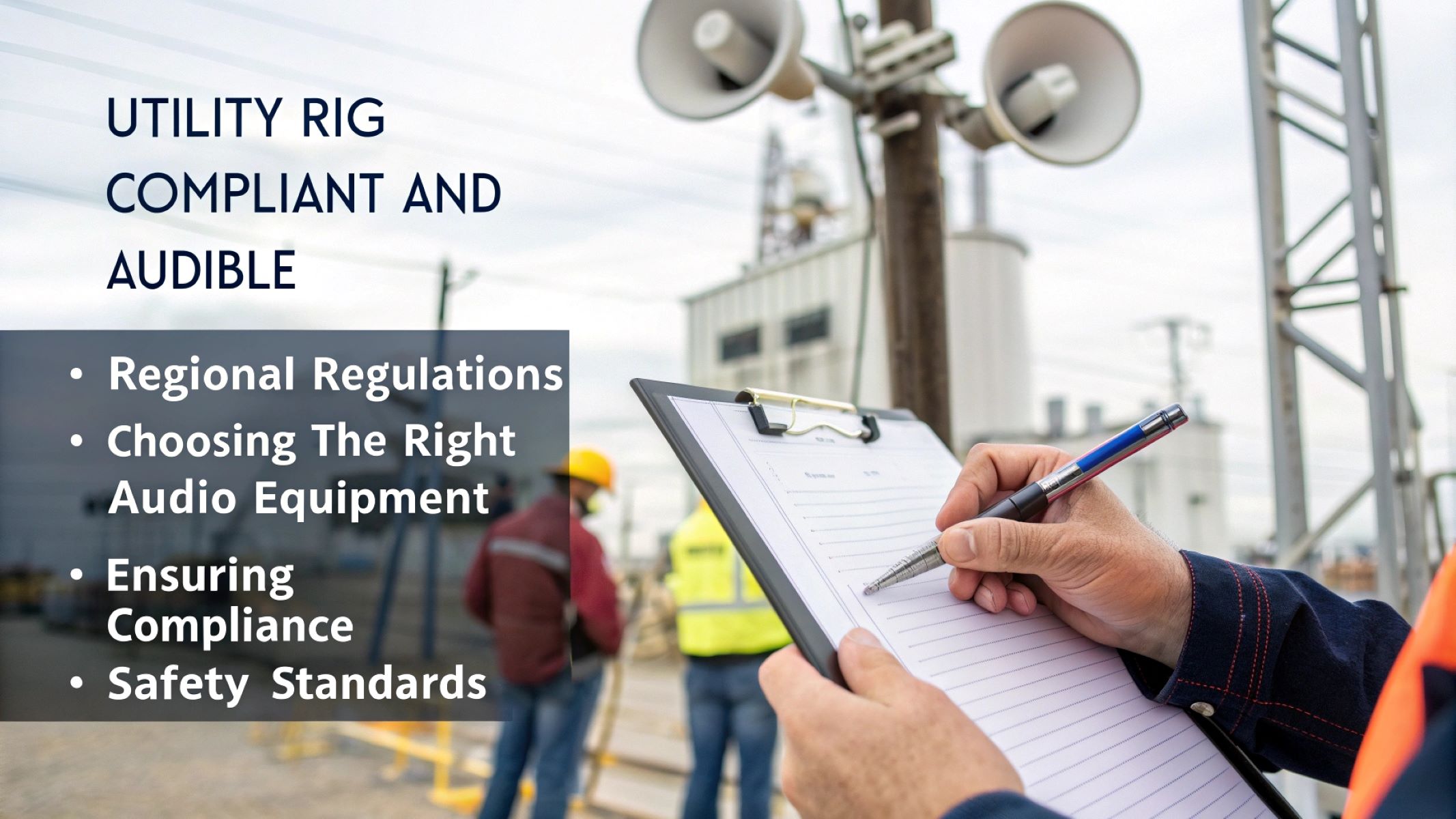
Ever wondered why some utility rigs sound louder, clearer, and still pass all the regulations? It’s not magic—it’s compliance and audibility working together. Utility rigs are crucial for communication in construction sites, utilities, and emergency services. Ensuring that your rig is compliant with safety and sound regulations while remaining audible can make a huge difference in effectiveness and safety. In this article, we’re diving deep into how you can make your utility rig both compliant and audible, keeping you safe and heard.
Understanding Utility Rig Compliance
Before diving into how to make your utility rig compliant and audible, it’s crucial to grasp what compliance really means in this context. Utility rig compliance involves following a set of regulatory standards and industry guidelines designed to ensure that your rig operates safely, effectively, and with minimal negative impact on the environment. These regulations come from authorities such as OSHA (Occupational Safety and Health Administration), EPA (Environmental Protection Agency), and local government bodies. The goal of compliance is to create a safe working environment for operators and those nearby, while also keeping your rig within legal and ethical boundaries.
Compliance covers several key areas that must be addressed when designing, operating, and maintaining a utility rig. Noise regulations set limits on how loud the rig can be, aiming to protect workers’ hearing and prevent noise pollution. Safety features, including lighting, signaling devices, and alarms, are mandatory to ensure the rig is visible and can effectively communicate warnings or operational status. Environmental regulations focus on controlling emissions and encouraging energy-efficient operations to reduce the rig’s ecological footprint. Lastly, operational standards guarantee that communication devices and other systems work reliably, ensuring smooth coordination on site.
The importance of compliance goes far beyond simply avoiding fines or legal trouble. At its core, compliance safeguards the health and well-being of everyone on and around the job site, particularly by limiting exposure to harmful noise levels that could cause hearing loss over time. It also contributes to overall operational efficiency by ensuring that all safety and communication systems are functioning correctly, which can reduce accidents and downtime. Moreover, compliance helps maintain good community relations by minimizing noise disturbances and environmental harm, which can otherwise lead to complaints or restrictions on operations.
In summary, utility rig compliance is a multi-faceted responsibility that balances safety, legal obligations, environmental concerns, and operational needs. When a rig meets these compliance standards, it not only protects workers and the environment but also supports smoother, more efficient project execution. Understanding these requirements thoroughly is the first step to making sure your utility rig is both compliant and effective in its role.
Making Your Utility Rig Audible
Factor | Description | Impact on Audibility | Challenges | Solutions |
Speaker Quality | Uses high-fidelity speakers that produce clear sound | Improves clarity and reduces distortion | Low-quality speakers produce muffled sound | Invest in durable, high-quality speakers |
Volume Levels | Sound output adjustable within legal limits | Ensures sound is loud enough without causing harm | Too low volume gets lost; too high causes distortion and legal issues | Calibrate volume using sound meters |
Sound Frequency | Certain frequencies travel better in outdoor spaces | Medium frequencies carry farther; very high or low may be absorbed | Low frequencies can be muffled by barriers | Choose frequency ranges optimized for site |
Ambient Noise | Background sounds like machinery and traffic | Can drown out or mask rig sounds | High ambient noise makes hearing alerts difficult | Use louder or directional speakers |
Acoustic Design | Directional vs. omnidirectional speakers | Directional focus improves sound targeting | Omnidirectional speakers waste energy, less focused sound | Position speakers to direct sound where needed |
Step-By-Step Guide to Making Your Utility Rig Compliant and Audible
Ready to upgrade your utility rig? Follow this detailed step-by-step list to ensure your rig meets compliance standards and remains clearly audible in all working conditions.
- Understand the Regulations for Your Region
Start by researching the noise and safety rules that apply to your area. This includes reviewing guidelines from OSHA, EPA, and any local or state authorities. Know the maximum permissible noise levels for your rig, typically measured in decibels, to avoid fines and ensure worker safety. - Choose the Right Audio Equipment
Selecting the proper speakers and audio devices is critical. Look for equipment with a wide frequency range to deliver clear sound, enough power output to be heard in noisy environments, and weatherproof features to withstand outdoor conditions. Directional speakers help focus sound where it’s needed most. Make sure all equipment is certified for compliance with noise and safety standards. - Install Sound Dampening or Acoustic Treatments
It may seem odd, but adding acoustic treatments can enhance clarity by reducing unwanted echoes and sound reflections. Use acoustic panels especially in enclosed spaces, install directional sound emitters, and carefully position speakers away from reflective surfaces like walls or metal structures to optimize sound delivery. - Calibrate Your Volume Levels Properly
Set your volume so it’s loud enough to be heard but not so loud that it risks hearing damage or breaks legal limits. Use sound level meters to measure output accurately and adjust the volume to peak just below the maximum allowed decibel level. Train your operators to understand and maintain these volume settings consistently. - Ensure Proper Signaling Devices Are Installed
Equip your rig with horns, sirens, or beacons that meet audibility and visibility standards. Choose signals with adjustable tones and volumes so they can be tailored to different noise environments. Make sure signals are audible above background noise and positioned where they won’t be blocked by equipment or other obstacles. - Perform Regular Maintenance and Testing
Compliance isn’t a one-time task; it requires ongoing attention. Regularly test all audio devices to ensure they work correctly, inspect wiring and speakers for corrosion or damage, and keep software or firmware updated on any smart audio systems. Replace any worn-out or malfunctioning parts quickly to maintain reliability. - Train Staff on Compliance and Audibility Protocols
Educate everyone who operates or works near the utility rig on the importance of maintaining compliance and keeping the rig audible. Training should cover volume calibration, equipment care, and recognizing when adjustments or repairs are needed.
Understanding the Science Behind Sound and Compliance
To truly optimize your utility rig’s audibility while staying compliant, it helps to have a basic grasp of how sound works in real-world environments. Sound travels in waves that interact with everything around them—surfaces, weather, and temperature all influence how sound moves and how well it can be heard. For example, when sound waves hit hard surfaces like concrete or metal, they tend to bounce back, creating echoes that can muddle the original signal. On windy days, sound can be carried away or distorted, making it harder for listeners to catch the full message. Even temperature plays a role; warmer air can help sound travel farther and clearer, while colder air can reduce clarity and speed.
Frequency—the pitch of the sound—is another critical factor in audibility. High-frequency sounds tend to be easier for people to locate because our ears can detect where these sounds come from more precisely. However, these higher frequencies also get absorbed more easily by obstacles such as walls or heavy machinery, limiting how far they travel. On the other hand, lower frequencies can move farther through barriers and over long distances, but they often sound muffled or less distinct. Finding the right balance between high and low frequencies in your rig’s audio output is essential for making sure your signals are both clear and far-reaching in noisy or cluttered work sites.
Sound levels and hearing safety are intertwined concerns when working with utility rigs. Prolonged exposure to loud noise can cause irreversible hearing damage, a risk that safety regulations take very seriously. OSHA, for instance, limits worker exposure to noise at or above 90 decibels for an eight-hour workday to protect hearing health. If sound levels exceed this threshold, employers must implement measures like hearing protection or reduce exposure time. This safety consideration is why making your rig audible does not simply mean blasting it as loud as possible—it’s about hitting the sweet spot where your alerts can be heard clearly without endangering anyone’s hearing.
Understanding the physics of sound and the safety limits helps you strike the right balance between audibility and compliance. It ensures your utility rig not only meets legal requirements but also provides clear, effective communication without putting workers at risk. This foundation allows you to make smarter choices about speaker types, volume levels, and signal frequencies, ultimately creating a safer and more efficient working environment.
Tips and Tricks to Enhance Your Utility Rig’s Performance
Tip | Description | Benefit | Implementation Considerations | Potential Challenges |
Use Directional Speakers | Focus sound toward specific areas instead of broadcasting widely. Like a flashlight beam, it directs sound efficiently. | Improves clarity and reduces noise pollution | Requires careful positioning and aiming of speakers | May need multiple units for full coverage |
Implement Visual Alerts | Combine audio signals with flashing beacons or lights to reinforce alerts. | Ensures alerts are noticed even in noisy or hearing-impaired situations | Needs power source and clear line of sight for visibility | Visual alerts might be less effective in bright daylight |
Train Staff for Effective Use | Educate operators about correct volume settings, compliance rules, and regular drills. | Maximizes equipment effectiveness and safety compliance | Requires ongoing training programs and refresher sessions | Staff turnover means constant retraining is necessary |
Comparing Common Utility Rig Audio Systems
Here’s a detailed, comprehensive list comparing the main types of audio systems used in utility rigs, covering their advantages, disadvantages, and compliance considerations:
- Horn and Siren Systems
- Pros:
- Extremely loud and clear, designed to cut through heavy background noise.
- Widely used and trusted for emergency alerts and warnings.
- Simple operation with immediate, recognizable sound patterns.
- Cons:
- Can be disruptive or annoying if overused, leading to worker fatigue or complaints.
- Limited to basic tones, lacking flexibility for complex messaging.
- Compliance Considerations:
- Must comply with local decibel regulations to prevent hearing damage.
- Requires periodic testing to ensure sound levels remain within legal limits.
- Public Address (PA) Systems
- Pros:
- Versatile, capable of broadcasting clear, intelligible speech and announcements.
- Allows communication of detailed instructions or safety information beyond simple alerts.
- Can cover large areas with multiple speakers for better site-wide communication.
- Cons:
- Volume may be insufficient in extremely noisy environments, reducing effectiveness.
- Needs regular calibration and maintenance to avoid degradation in sound quality.
- Installation can be more complex, requiring wiring and placement planning.
- Compliance Considerations:
- Must be carefully calibrated to avoid exceeding permissible noise levels.
- Needs routine checks to maintain compliance and performance.
- Digital Voice Systems
- Pros:
- Offers clear, adjustable sound quality with customizable tones and messages.
- Supports integration with digital safety and communication networks for enhanced control.
- Enables programmable alerts, remote operation, and advanced functionality.
- Cons:
- Setup and configuration can be technically complex, requiring trained personnel.
- Higher initial cost compared to analog systems.
- Dependent on software updates and compatibility checks.
- Compliance Considerations:
- Software and firmware must be regularly updated to meet evolving regulations.
- Requires monitoring to ensure consistent adherence to noise and safety standards.
- Pros:
- Pros:
- Pros: